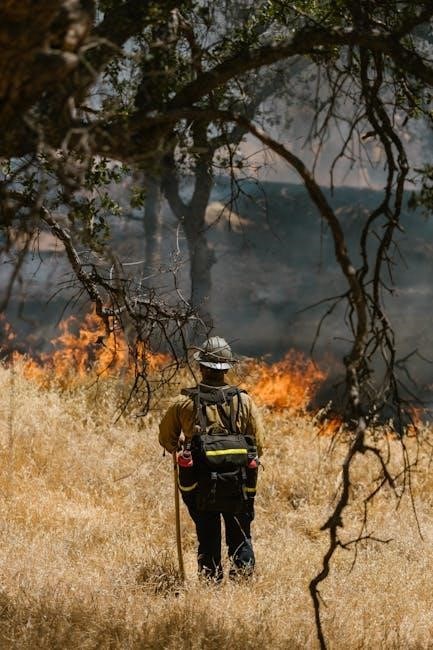
Manual handling risk assessment identifies tasks involving physical exertion, evaluating risks to prevent injuries. It ensures safe practices, reduces workplace accidents, and promotes employee well-being effectively. Key focus areas include task analysis, risk evaluation, and implementing controls to mitigate hazards, ensuring compliance with safety standards and regulations.
1.1. Definition and Importance
Manual handling risk assessment is a systematic process to identify and evaluate tasks involving physical exertion that could lead to injury. Its primary purpose is to prevent workplace injuries by analyzing lifting, carrying, and repetitive tasks. Importance lies in safeguarding employee health, reducing absenteeism, and ensuring legal compliance. By prioritizing safety, it fosters a culture of prevention, enhancing overall workplace efficiency and productivity while minimizing risks associated with manual labor.
1.2. Scope and Application in Workplaces
Manual handling risk assessment applies broadly across industries, from healthcare to manufacturing, targeting tasks that involve physical exertion. Its scope includes evaluating repetitive actions, lifting, pushing, and carrying, ensuring safe practices. Workplaces benefit by identifying high-risk tasks, reducing injuries, and improving employee safety. Regular assessments ensure compliance with safety standards, fostering a proactive approach to hazard management. This process is particularly vital in sectors with high manual labor demands, such as hospitals and logistics, to prevent work-related injuries and enhance overall workplace safety.
Legal and Regulatory Requirements
Manual handling is governed by regulations like the Manual Handling Operations Regulations 1992 and the Health and Safety at Work Act 1974. These laws require employers to conduct risk assessments, implement control measures, and provide employee training to minimize injuries and ensure compliance with safety standards.
2.1. Overview of Relevant Laws and Standards
Manual handling is regulated by laws such as the Health and Safety at Work Act 1974 and the Manual Handling Operations Regulations 1992. These laws mandate risk assessments and control measures to prevent injuries. Employers must ensure tasks are safely designed, and employees are trained. International standards like ISO 11228 and NIOSH guidelines also provide frameworks for assessing manual handling risks. Compliance with these regulations is essential to avoid legal penalties and promote workplace safety effectively.
2.2. Employer and Employee Responsibilities
Employers are responsible for conducting manual handling risk assessments, providing training, and implementing control measures. They must ensure tasks are safely designed and risks minimized. Employees must cooperate by following safe practices, reporting hazards, and attending training. Both parties share responsibility for maintaining a safe work environment. Employers must provide necessary resources, while employees must adhere to guidelines and use provided equipment. Collaboration is key to preventing injuries and ensuring compliance with legal requirements effectively.
The Risk Assessment Process
The risk assessment process involves evaluating manual handling tasks to identify, assess, and mitigate risks, ensuring safe working practices and regulatory compliance.
3.1. Identifying Manual Handling Operations
Manual handling operations involve tasks that require physical exertion, such as lifting, carrying, pushing, or pulling. These operations are often repetitive or involve awkward postures, increasing injury risks. Identifying such tasks is the first step in risk assessment, ensuring they are evaluated for potential hazards. This process helps prioritize tasks for further analysis and control measures, ultimately reducing workplace injuries and improving safety standards.
3.2. Assessing the Risks of Injury
Assessing the risks of injury involves evaluating the physical demands of manual handling tasks, such as force, posture, and repetition. Factors like task duration, environment, and individual worker capabilities are considered. This step identifies high-risk activities that could lead to musculoskeletal disorders or other injuries. By systematically analyzing these elements, organizations can rank risks and implement targeted controls to minimize harm and ensure a safer working environment for employees;
3.3. Prioritizing Controls and Interventions
Prioritizing controls and interventions involves ranking risk reduction measures based on effectiveness, feasibility, and compliance. A hierarchy of controls is applied, starting with eliminating hazardous tasks, followed by engineering solutions, administrative controls, and PPE as a last resort. Organizations should prioritize measures that reduce risks most effectively while considering practical implementation. This systematic approach ensures that the most critical risks are addressed first, minimizing workplace injuries and enhancing overall safety standards.
Control Measures for Manual Handling Risks
Control measures focus on eliminating or reducing risks through mechanical aids, task redesign, and administrative strategies. Prioritizing hazard elimination and implementing engineered solutions minimizes injury risks effectively.
4.1. Elimination of Hazardous Tasks
Eliminating hazardous tasks is the first step in managing manual handling risks. This involves identifying tasks that can be automated or replaced with mechanical aids, reducing the need for physical exertion. By removing high-risk operations, workplaces can significantly lower injury rates. Employers should assess tasks to determine if they can be redesigned or substituted with safer alternatives, prioritizing employee safety and well-being. This proactive approach minimizes risks before they occur, creating a safer work environment.
4.2. Engineering and Administrative Controls
Engineering controls involve modifying workstations or using mechanical aids to reduce manual handling risks. Administrative controls focus on policies like task rotation, workload management, and training programs. These measures aim to minimize physical demands and ensure safe work practices. By implementing ergonomic solutions and clear procedures, employers can significantly reduce injury risks. Regular reviews of these controls ensure ongoing effectiveness and adaptability to changing workplace demands, fostering a safer and more efficient work environment for all employees.
4.3. Personal Protective Equipment (PPE)
Personal Protective Equipment (PPE) plays a crucial role in reducing manual handling risks when other controls are insufficient. Common PPE includes gloves, back belts, and supportive footwear, designed to minimize strain and prevent injuries. Employers should ensure PPE is selected based on task-specific risks and properly fitted to individual employees. Training on correct usage and maintenance of PPE is essential to maximize its effectiveness. Regular updates to PPE policies ensure alignment with evolving safety standards and workplace demands, safeguarding employee health and productivity.
Training and Competency
Training programs ensure employees handle manual tasks safely, covering lifting, carrying, and repetitive tasks. Proper techniques reduce injuries and maintain compliance with workplace safety standards effectively.
5.1. Staff Training Programs
Staff training programs are essential for ensuring employees understand safe manual handling practices. These programs focus on proper lifting, carrying, and repetitive task techniques to minimize injuries. Training often includes practical demonstrations and assessments to verify competency. The goal is to empower employees with the knowledge and skills to perform tasks safely, reducing workplace accidents and promoting a culture of safety. Regular updates and refreshers are crucial to maintain high standards of manual handling practices across all departments.
5.2. Assessing Employee Competency
Assessing employee competency ensures staff can safely perform manual handling tasks. This involves practical tests, observations, and written evaluations to verify understanding and adherence to safe practices. Employers must document assessments to confirm competency, providing feedback for improvement. Regular reassessments are essential to maintain standards and adapt to new practices or equipment; Competency assessments ensure employees are proficient in manual handling, reducing injury risks and fostering a safer workplace environment. This step is critical for sustained compliance with safety protocols and regulations.
Case Studies and Examples
A hospital implemented a manual handling consultative team, reducing injuries by 30% through improved task analysis and staff training, showcasing effective risk management strategies in action.
6.1. Successful Risk Reduction Strategies
Effective strategies include task analysis, staff training, and mechanical aids. A hospital reduced injuries by 30% using a consultative team. Another workplace replaced heavy carts with automated systems, cutting injuries by 25%. These examples highlight the importance of proactive measures and employee engagement in achieving sustainable risk reduction.
6.2. Lessons Learned from Workplace Incidents
Workplace incidents reveal common causes of manual handling injuries, such as poor training, ergonomic neglect, and inadequate risk assessments. A hospital incident highlighted the need for better staff training, reducing injuries by 30% post-intervention. Another case showed that ignoring ergonomic principles led to repetitive strain injuries. These lessons emphasize the importance of proactive risk assessments, employee training, and ergonomic adjustments to prevent future incidents and ensure a safer work environment.
Tools and Resources
Manual handling risk assessment tools include templates, checklists, and software to streamline evaluations. These resources help identify hazards, assess risks, and implement effective control measures efficiently, ensuring compliance and safety.
7.1. Manual Handling Risk Assessment Templates
Manual handling risk assessment templates provide structured frameworks to identify and evaluate hazards. They include sections for task description, risk factors, and control measures. These tools help organizations systematically assess lifting, carrying, and repetitive tasks, ensuring compliance with safety standards. Templates often feature checklists, risk scoring, and action plans. By using these resources, employers can document findings, prioritize interventions, and maintain records for audits. They are essential for creating a robust risk management process and promoting a safer work environment.
7.2. Software and Apps for Risk Management
Software and apps for manual handling risk management streamline the assessment process with digital tools. These platforms offer features like automated risk scoring, real-time data collection, and reporting. Mobile apps enable employees to conduct on-site assessments efficiently, while cloud-based systems ensure data accessibility. Advanced software incorporates AI to analyze trends and predict potential risks. These tools enhance accuracy, reduce administrative burdens, and facilitate proactive risk management, making them indispensable for modern workplace safety programs and compliance with regulatory standards.
Manual handling risk assessment is crucial for preventing injuries and ensuring workplace safety. Future trends include advanced scoring systems and evolving safety standards, enhancing risk management strategies globally.
8.1. The Evolving Landscape of Manual Handling Safety
Manual handling safety is continuously evolving, with advancements in technology and data analytics reshaping risk assessment practices. New scoring systems and post-fall protocols are being integrated to enhance safety standards. The use of artificial intelligence and IoT devices is expected to play a significant role in monitoring and preventing manual handling injuries. These innovations aim to create safer workplaces by identifying high-risk tasks more effectively and promoting proactive interventions. Collaboration between industries and researchers is driving these improvements forward.
8.2. Best Practices for Sustained Compliance
Best practices for sustained compliance involve regular training updates, proactive risk assessments, and continuous monitoring of manual handling tasks. Employers should prioritize staff involvement in risk reduction strategies and ensure tasks are designed to minimize physical strain. Guideline applications and consultative teams play a crucial role in maintaining safety standards. By fostering a culture of awareness and accountability, organizations can achieve long-term compliance with manual handling regulations and reduce workplace injuries effectively.